Food Service Kiosks
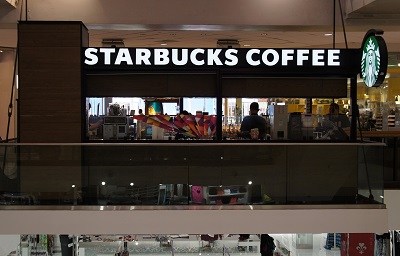
I began work at Synsor Corporation in 2012 when I joined a team that was focused on maintaining the Starbucks Kiosk program as a Product Engineer. I was tasked by the project lead with engineering parts to help fulfill orders and create models for the standard catalog of countertops, cabinets, and decorative wood panels. Fresh out of college, this work taught me the basic manufacturing processes for wood, metal, and solid surface.
After a few months, Starbucks was looking to create an updated kiosk design that would serve as the basis of their program and selected Synsor to help develop the layout. We developed a custom extrusion for some of the visual elements and brought in a structural engineer to recommend changes and approve the integrity of the standalone kiosk. In keeping with lean manufacturing concepts, we attempted to reuse parts from the old layout as much as possible and even built the core frame in the same way so that the shop would not need extensive retraining on how to wire and plumb it.
I became the project lead shortly after the launch of the new kiosk layout. At this point, I had two primary tasks. For the program as a whole, I was in charge of receiving feedback from the shop and finding fixes or applying changes. Because we bought metal pieces in bulk, it was often necessary to find a short-term modification for our existing inventory while at the same time making sure that the next round of orders sufficiently addressed the issue.
My other work involved the customization of the standard layouts we had developed for specific sites. The reasons for these customizations often involved site-specific challenges, landlord requirements, and local health codes. In one particular instance, we had to powder coat all of the standard black metal to a light gray and attach a security screen to the underside of the canopy. For another project, we cut the canopy metal so that the kiosk could fit beneath an escalator. Another time, we placed two canopies side by side but replaced the food service interior for one of them with banquettes and tables for customers.
During this time, the project team grew to five engineers and drafters, including one remote worker. Many of them were new to the company, so I was tasked with teaching them about best practices for modeling and the workflow for getting projects approved and sent off for manufacturing. In the same way that I began, I had them assemble layouts for client drawings.
A few years later, we again were selected to develop a new kiosk layout. This time, as the program lead, I was in charge of working with Starbucks to make sure that the design was both functional and visually appealing. I also applied the knowledge I had gained about MEPs to develop a basic set that could be reviewed and signed off by a licensed engineer.
Because I had been on the project during the last layout development, I understood the challenges we faced during the last rollout. At times, it had been hectic supporting the new program because the standard catalog had not been fully modeled, and as a result we were assembling several kiosks from scratch at the same time. Learning from this, I ensured that the full catalog of parts was completed by the beginning of the new program launch, and several sample template kiosks were built with attached drawing sets so that they would be easy to pull from and subsequently modify.